When we meet with future clients, they are usually comparing several types of roofing systems. We are always asked: Which is better? Which is more affordable? Which is best for long lasting protection?
At West Roofing Systems, we want to make sure that our future clients have the best information available. For this reason, we created an article that explores the differences between single-ply membrane and built-up roofing systems to give you all the information you need in choosing which roof for your facility.
The Basics
Single-Ply Membrane Roofing
[caption id="attachment_24401" align="alignright" width="300"]
Single-Ply Membrane Roofing[/caption]
Single-Ply Membranes are sheets of rubber and other synthetics that can be chemically adhered to insulation or ballasted creating a layer of protection on your commercial facility.
There are two main types of single-ply membrane commercial roofing: Thermoplastic Polyolefin (TPO) and Ethylene Propylene Diene Terpolymer (EPDM). They differ in their chemical makeup, how they are installed and the energy efficiency.
Read More: Single-Ply Membrane Roofing: Installation & Performance
Built-Up Roofing
Built-Up Roofing Systems have been in use in the U.S. for over 100 years. These roof systems are commonly referred to as "tar and gravel" roofs. Built-up systems are installed by alternating layers of asphalt or tar and supporting fabrics directly onto the roof. You can choose the number of layers (or plies) that are installed. The final layer of a built-up roofing system consists of stone or gravel.
Cost
Single-Ply Membrane Roofing
For an average 20,000 sq. foot commercial roof, it will usually cost between $3.50 to $7.50 per square foot for EPDM and $3.50 to $6.50 per square foot for TPO, including materials and labor warranty.
Read More: Cost of Single-Ply Membrane Roofing
[caption id="attachment_23885" align="alignright" width="300"]
Tar and Gravel Roofing[/caption]
Built-Up Roofing
For an average commercial roof, it will usually cost between per $5.50 - $8.50 square foot in materials and labor to install a typical built-up roofing system. This price range can change depending on the materials you choose.
Installation
Single-Ply Membrane Roofing
The beginning of the installation process is similar between TPO and EPDM single-ply membrane roofing systems.
After the existing substrate is prepared, either by cleaning or removing the existing roof, the insulation is installed. There are a few types of insulation options the facility manager/owner can choose from Polyisocyanurate (Polyiso), Expanded Polystyrene (EPS), Extruded Polystyrene (XPS)
After the existing substrate is prepared, either by cleaning or removing the existing roof, the insulation layers are installed and covered by a cover board.
There are three ways to attach the membrane to the cover board: ballasted, with an adhesive or mechanically fastened.
The significant difference between TPO and EPDM comes when it is time to adhere the membrane seams together. TPO uses a hot-air gun to melt down the membrane at the seams and fuse them together. EPDM is joined together with a seam tape.
Infographic: Single-Ply Membrane Roofing: TPO vs EPDM
Built-Up Roofing
The first layer can be adhered directly to the roof substrate. If needed, a base sheet can be fastened to the roof to create a flat and safe work space. A built-up roofing system is installed by alternating layers of bitumen and reinforced fabric. Property managers can choose three, four or five ply roofs to meet their needs and budgets.
The last layer is rock or stone, this layer protects the underlying layers from UV rays, extreme heat or cold, and wind damage. A layer of gravel can be added to be more aesthetically appealing.
Advantages
[caption id="attachment_23972" align="alignright" width="300"]
EPDM Single-Ply Roofing System[/caption]
Single-Ply Membrane Roofing
If properly installed and maintained, a commercial single-ply membrane roof can last 30 years. There are quite a few other benefits of single-ply membrane roofing systems:
- Proven Track Record - EPDM roofing has been used for commercial flat roofing for over 60 decades. This amount of time on the market has allowed various laboratory and field studies to be performed and tracked.
- Customer Choice of Insulation - Since single-ply membrane roofing does not include the insulation factor, as a customer you have more options to choose from to insulate your facility’s roof.
- Class A Fire-Rated - TPO membranes and EPDM can achieve Underwriters Laboratories (UL) Class A fire resistance listings by adding fire retardant chemicals during the manufacturing process.
- Reflective or Retentive - TPO is generally white and highly reflective. On the other side of the spectrum, EPDM is often described as “Black Roofs,” due to the natural dark color of the membrane.
Read More: Pros and Cons of Single-Ply Membrane Roofing Systems
Built-Up Roofing
If properly installed and maintained, a commercial built-up roof can last 40 years. There are a few other benefits of built-up roofing systems:
- Seamless and Waterproof - The continuous solid surface does not require joints or seams, removing the most vulnerable area for leaking.
- Reflects UV Rays - provides ultra-violet protection.
- Low- maintenance – Minimal upkeep needed after installation.
Read More: Asphalt Roofing Manufacturers Association
Disadvantages
Single-Ply Membrane Roofing
While the advantages of a single-ply membrane roofing system outweigh the disadvantages, there are a few things you should keep in mind. Here are disadvantages of single-ply membrane roofing systems:
- Durability - Single-ply membrane roofing does not have a hard top layer to protect the synthetic rubber from dropped tools, gravel or loose screws from being pushed into the rubber membrane.
- Seams - Although these seams are sealed either mechanically or with melting adhesives, they are still areas that are more vulnerable to leaks than other roofing systems.
- Roofing Accessories – Penetrations such as skylights or vents need special attention during installation.
- UV Rays - UV rays that shine directly on the roof can degrade the adhesives quickly over time.
[caption id="attachment_23977" align="alignright" width="300"]
TPO Single-Ply Membrane Roofing[/caption]
Built-Up Roofing
Built-up roofing systems have been around for decades; their longevity can only be obtained if the roof is maintained properly. Here are other disadvantages of built-up roofing systems:
- Time - Slower installation time frame
- Safety - Hazardous fumes and vapors when installing it
- Weight – Adds extra weight to the building structure
- Costs – Installation costs
- UV Rays – Without the gravel top layer, UV rays can break down the membrane quickly
As you can see, both Single-Ply Membrane and Built-Up Roofing Systems have their benefits and drawbacks. Choosing which one is best comes down to a customer-by-customer basis.
West Roofing Systems, Inc. installs sustainable and efficient roofing systems for commercial, industrial, manufacturing and municipal buildings. In over 37 years, we have installed over 56,000,000 square feet of commercial Spray polyurethane foam (SPF), single ply membrane and other popular roofing systems.
If you are looking for maintenance, repair or replacement for your facilities roof, fill out our quote form for your free no-obligation commercial roof quote from our team of experts.
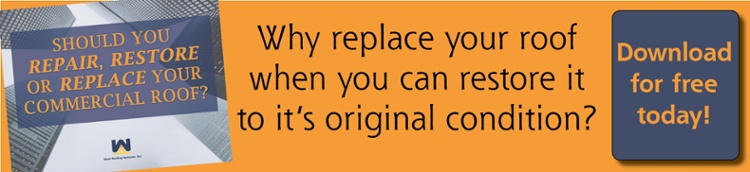
Article Here: Single-Ply Membrane vs Built-Up Roofing: Which is Best for Commercial Roofs?