Whether you’re installing a new commercial roof or taking care of an existing system, it's important to maintain your roof regularly and address problems quickly. You may not know you have a problem with your roof until you see signs inside your building, such as brown spots on your ceiling or puddles on your floor. These are signs that you need to have someone inspect and repair your commercial roof immediately.
Read More: Commercial Roof Maintenance 101
At West Roofing Systems, we take pride in the new roofs we install and the maintenance we provide for our customers and their commercial, industrial and manufacturing buildings. Our M.a.R.S. (Maintenance and Repair Service) Program is available for new and existing roof systems.
[caption id="attachment_23923" align="alignright" width="300"]
Roof Leak in Office Building[/caption]
Our technicians answer many questions from facility owners and managers. One question we often get is, “What are these brown spots on my ceiling?” That’s why we wrote this article to show you what water stains are, the dangers of water stains and how to repair your facility.
What Are Brown Spots on My Ceiling?
When you see brown spots, or patches, on your ceiling and interior walls, they are water stains caused from a leak above. This leak could be a malfunction in your commercial roof systems or a leak with another part of your facility such as HVAC units or leaking pipes.
Common Causes of Water Stains
There are a few causes that we commonly find while inspecting internal leaks that cause water stains. Some are caused by a failure of the roof, but there are also many other reasons that water is leaking into your building.
Read More: Common Causes of Roof Leaks
Vents/Skylights
[caption id="attachment_23979" align="alignright" width="300"]
TPO Single-Ply Membrane around Roof Penetration[/caption]
Most commercial roofing systems have accessories attached such as skylights, air vents, plumbing vents and more. To accommodate for these units, your contractor needs to cut their roofing material to fit around the unit. These areas are not seamless roofing material, so they are vulnerable to leaks through the penetrations. This problem will show when you have stains around vents or skylights in particular.
HVAC Units
HVAC units can cause issues in a few ways:
- Improper installation around the HVAC unit
- Water leaking from the actual HVAC unit (not a roofing problem in this case)
- Water leaking from the unit on top of the roof causing problems if it doesn’t drain properly
Whether you call your roofing or HVAC contractor, they should be able to help you narrow down the cause of your HVAC area leak.
Leaking Pipe
Sometimes water stains are not caused by a roof issue at all. Leaking pipes in ceilings and walls can slowly drip water until a stain appears in your building. Pipes can be prone to leaks when they are aged and with extreme changes in temperature.
Roof Flashing Failure
Flashings are pieces of metal that are installed on a roof where two areas join together. The purpose of these metal pieces is to prevent water from leaking through the vulnerable area. Since the area underneath is at risk of leaking, it’s essential to keep your metals flashings in proper working order.
If there is a failure with your flashings, water may be able to leak not only through your roof, but you will often see water stains down walls as well.
Damaged or Aged Waterproofing Membrane
The membrane of a commercial roof is the waterproof layer. When there is damage to the membrane from the weather, foot traffic, mechanical damage or any other numerous situations, it can allow water to leak through the waterproof membrane and saturate the underlying insulation.
Most commercial roofing systems last between 15 and 20 years; this lifespan can vary depending on the type of roof you install on your facility. The older a roof is, the less reliable it can be for leaks. While enrolling in a roof maintenance plan can extend the lifespan of your roof, after a certain number of years, it’s time to replace your roof system.
Download: Commercial Roofing 101
How to Repair Water Stains
The quicker you are in responding to your water stain, the better it will be repairing it. Your first step is to address the cause of the stain. If you only address the water stain without fixing the cause, it will not only reappear, but it will cause more damage in the long run.
The extent of your repair depends on the amount of damage your facility has sustained. Hopefully, you caught the problem early and took action quickly. Some options to repair and clean up water stains include:
- Use a bleach/water solution to blot and wipe the stain away
- After the area dries, if it is still stable, you can directly paint over the area
- Remove the damaged part of the ceiling/ceiling tiles, drywall and replace with new, clean sections
- Sand off the damaged layer and seal the area (wood ceiling)
Watch for Mold
If your stains have yellow or green colors, chances are you have mold in that area as well. As mold grows, it becomes darker and more dangerous over time. If you have mold in your facility, you need to take action right away for the safety of everyone in your building. Mold needs to be killed, whether it is a simple bleach/water mix or if you have to call a mold removal company.
Read More: EPA Mold Remediation in Schools and Commercial Buildings Guide
Investing in a commercial roofing project can be a daunting task. But by being prepared and asking the right questions, you can find the right contractor to deliver high-quality work at the right price.
Choosing West Roofing Systems as a turnkey roofing company will provide you with highly trained teams and award-winning service. Our services are flexible and diverse; we can recoat, repair or replace your facility’s roof so that it lasts decades.
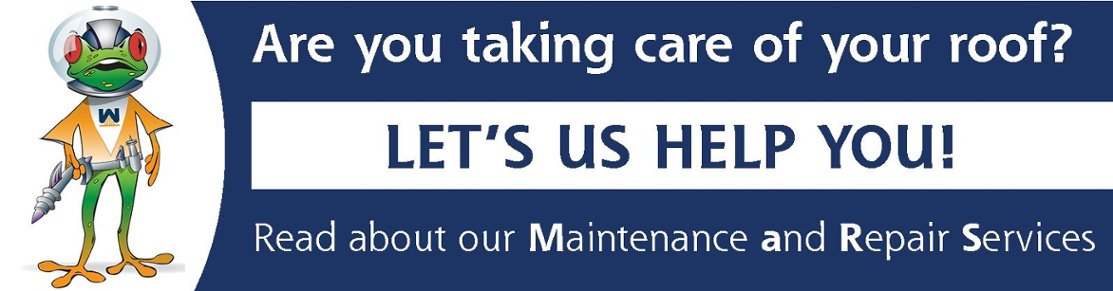
Read More:
Original Post Here: Got Brown Spots on Your Ceiling? Causes & Solutions for Water Stains